Wednesday, December 25, 2019
Friday, December 20, 2019
New airball, who dis?
My friend Sergey is testing Airball with noobs and students on N291DR, and has some really interesting feedback. One thing he noticed is that, if it is to be "seen" by peripheral vision, then it should have contrast, because our peripheral vision does not see color. He also asked for the IAS to be visible in the ball somewhere. I added these in and this is the result:
Meanwhile, there are strange developments in the shop, wherein crufty 3D printed parts are being connected to one another. Stay tuned!
Meanwhile, there are strange developments in the shop, wherein crufty 3D printed parts are being connected to one another. Stay tuned!
Sunday, December 1, 2019
Turkey eating weekend developments
We drove from San Jose to Mendocino to hang out with family this weekend for Thanksgiving. I thought about flying KRHV KLLR but ... I'm glad I didn't. The weather here in Northern California is a total mess. This is the atmospheric river that is dumping on us:
This is what the sky looks like from the back of the workshop this afternoon.
Since these turkeys are not going to eat themselves, developments on Airball have been modest -- but they have been steady. We now have a little contraption, made of 4 potentiometers and a bit of Arduino widgetry on a piece of cardboard. The inputs are (α, β, q, ρ) where:
By messing with the dials, the widget sends the same wireless signals as an actual Airball probe would given the same airdata. And then that shows up on a generic Airball display!This is what the sky looks like from the back of the workshop this afternoon.
Since these turkeys are not going to eat themselves, developments on Airball have been modest -- but they have been steady. We now have a little contraption, made of 4 potentiometers and a bit of Arduino widgetry on a piece of cardboard. The inputs are (α, β, q, ρ) where:
α = angle of attack
β = angle of yaw
q = dynamic pressure
ρ = air density
It's all a bit jury-rigged for now but we have plans for this as a demonstration and education tool.
Meanwhile, we have two displays sitting in the workshop: one working (the one you see above) and another one that needs its screen replaced:
We have two complete "kits" for two probes, with all 3D printed and electronic parts, missing only the tubing and screws:
Finally, we are working on a new, leaner, meaner version of our strut mounts, this time trying to make them generic "V" blocks so they fit on almost any wing strut. This is one very early prototype and the 3D printed parts for the next iteration:
Stay tuned for build pictures of the next two probes, and details of the development of the new strut mounts.
Saturday, November 16, 2019
Two more display modules
Today I finished two more display modules.
One of them uses one of the new XBee 3 wireless modules. It initially didn't work with the XBee 2 that I had, until I realized I needed to install the 802.14 firmware. Once I did that, it was plug-and-play compatible with both hardware and software.
The most crufty part of the build is the tiny resistor network which provides reliable pullup and pulldown voltages for the quadrature encoder knob. I tried using the internal Raspberry Pi GPIO pullups for that purpose, but they don't seem to push enough current to produce reliable results when turning the knob quickly. So resistor network we must have. If I were to make this design in any quantity, I would spin up a PCB for that tiny thing -- but right now the protoboard is adequate. I am not sure the brightness of these displays is where I need it to be anyway, so I hesitate to "standardize" on this design.
Here are some build photos for your enjoyment.
One of them uses one of the new XBee 3 wireless modules. It initially didn't work with the XBee 2 that I had, until I realized I needed to install the 802.14 firmware. Once I did that, it was plug-and-play compatible with both hardware and software.
The most crufty part of the build is the tiny resistor network which provides reliable pullup and pulldown voltages for the quadrature encoder knob. I tried using the internal Raspberry Pi GPIO pullups for that purpose, but they don't seem to push enough current to produce reliable results when turning the knob quickly. So resistor network we must have. If I were to make this design in any quantity, I would spin up a PCB for that tiny thing -- but right now the protoboard is adequate. I am not sure the brightness of these displays is where I need it to be anyway, so I hesitate to "standardize" on this design.
Here are some build photos for your enjoyment.
Saturday, November 9, 2019
Cold solder is cold
After a CAD session during which vibration isolating versions of the probe board mounting areas were designed, I looked at the miserable board to see if I could determine the cause of failure. Well, it turns out I had a cold solder joint for the GND connection to the power and battery management daughterboard.
This is the solder joint in question, in the PCB hole pointed to by the screwdriver:
I did not allow for enough heating when applying the solder, and must have done a poor job of inspecting the board because, in hindsight, the joint in the photo looks pretty bad -- it's obviously just a bleb of solder sitting there.
In the same orientation, this is the hole in the PCB layout. You can see that it is properly joined to the ground plane by thermals, to alleviate exactly this problem:
So we're back on track -- but, if I can, I will change to the vibration isolated version of my mounting, just in case. If it's not too much more trouble, it should be really helpful.
This is the solder joint in question, in the PCB hole pointed to by the screwdriver:
I did not allow for enough heating when applying the solder, and must have done a poor job of inspecting the board because, in hindsight, the joint in the photo looks pretty bad -- it's obviously just a bleb of solder sitting there.
In the same orientation, this is the hole in the PCB layout. You can see that it is properly joined to the ground plane by thermals, to alleviate exactly this problem:
So we're back on track -- but, if I can, I will change to the vibration isolated version of my mounting, just in case. If it's not too much more trouble, it should be really helpful.
Vibration damage in avionics is a thing (who knew?)
The Airball probe stopped working a few days ago while I was taxiing N291DR along the gopher-hole-pitted grass runway at the Monterey Bay Academy airport (CA66).
If you don't know this, the Monterey Bay Academy is a Seventh Day Adventist boarding high school in our region. They have an airport (of course! which self-respecting boarding high school doesn't?). And they have for years very generously made it available to the flying community, so long as you respect their rules -- mainly, refraining from landing during the Sabbath. They are awesome folks.
I have been working up to landing at their strip, which is sort of a "bush flying kindergarten". A few days ago, accompanied by my wife (and Airball Product Marketing Manager) Melissa Blum, I landed there as PIC for the first time ever!
Airball worked fine, until we did the long back-taxi down the bumpy runway. Then it stopped sending data. It's been a few days since I had the chance to pull it off the airplane and debug, but now I think I know what happened.
In this video, you will see that merely by wiggling the Pro Micro Arduino daughterboard, I can get it to turn off and on. So basically, the power supply solder connections or circuit board traces were mechanically damaged by the bumpy taxi!!
I found this out when I was poking around the circuit with my test probes and just happened to notice that the act of poking with the probes itself got the thing to light up and start flickering and sending data. Here is the video:
So the realization du jour is: Vibration in avionics is a thing.
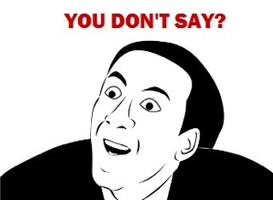
Clearly I need to redesign my probe somewhat to add rubber vibration isolators to the board mount. This is a bit of a pain in the neck as I had hoped to be done with futzing with the probe mechanical design, to be perfectly honest. But I have to do what I have to do.
I hope I can manage to get some sort of isolation mount for the rear of the board. As you can see in the video, that area is already pretty "busy" and is not designed with any sort of simple mounting holes.
If you don't know this, the Monterey Bay Academy is a Seventh Day Adventist boarding high school in our region. They have an airport (of course! which self-respecting boarding high school doesn't?). And they have for years very generously made it available to the flying community, so long as you respect their rules -- mainly, refraining from landing during the Sabbath. They are awesome folks.
I have been working up to landing at their strip, which is sort of a "bush flying kindergarten". A few days ago, accompanied by my wife (and Airball Product Marketing Manager) Melissa Blum, I landed there as PIC for the first time ever!
Airball worked fine, until we did the long back-taxi down the bumpy runway. Then it stopped sending data. It's been a few days since I had the chance to pull it off the airplane and debug, but now I think I know what happened.
In this video, you will see that merely by wiggling the Pro Micro Arduino daughterboard, I can get it to turn off and on. So basically, the power supply solder connections or circuit board traces were mechanically damaged by the bumpy taxi!!
I found this out when I was poking around the circuit with my test probes and just happened to notice that the act of poking with the probes itself got the thing to light up and start flickering and sending data. Here is the video:
So the realization du jour is: Vibration in avionics is a thing.
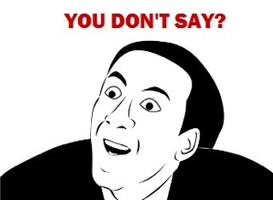
Clearly I need to redesign my probe somewhat to add rubber vibration isolators to the board mount. This is a bit of a pain in the neck as I had hoped to be done with futzing with the probe mechanical design, to be perfectly honest. But I have to do what I have to do.
I hope I can manage to get some sort of isolation mount for the rear of the board. As you can see in the video, that area is already pretty "busy" and is not designed with any sort of simple mounting holes.
Monday, October 28, 2019
Inventory time
Apart from what's in N291DR at the moment, I hope to build 2 more Airball systems. This the inventory of components I have so far for the two probes and displays:
Stay tuned as these get built up. It should be possible, I think, to show the work being "kitted up" much more clearly this time now that we have been around this block a few times.
Saturday, October 26, 2019
Successful test flight, good performance
Today I flew the latest Airball hardware on N291DR, and it worked beautifully!!! In particular, as I was calibrating the airspeeds, I noted that I was getting VFE = 70 kias at exactly the same point as the airplane's built-in airspeed indicator. Stall was predictable, yaw was consistent with the inclinometer, there was no "lag", and overall things were peachy!
Unfortunately we are using a commodity LCD panel which is not as bright as some others we've tried, so I can't show you any video! It washed out completely! Maybe I'll share a video of me flying with it just for fun though.
Here are some photos of the installation.
Unfortunately we are using a commodity LCD panel which is not as bright as some others we've tried, so I can't show you any video! It washed out completely! Maybe I'll share a video of me flying with it just for fun though.
Here are some photos of the installation.
Saturday, October 19, 2019
New "maker" display is complete
Today I put together the first complete prototype of the "maker" style display -- one which uses commodity parts. There is a small resistor network for the encoder knob, which I made on a piece of breadboard -- that can be a tiny custom PCB at some point. Otherwise, this is built around a standard Raspberry Pi and a 4.3" HDMI LCD panel that's inexpensive and available everywhere. The result looks like this:
We still have a few software improvements / bugs before we get a test flight, but in the meantime, check out the assembly pictures!
We still have a few software improvements / bugs before we get a test flight, but in the meantime, check out the assembly pictures!
Wednesday, October 9, 2019
New probe has 12h battery life as previous
Just confirmed the new probe has a 12 hour battery life, comparable to our previous design. This is not surprising, given that it's just a recasting of the same hardware, but it's still good to know. Here is the probe sitting on my desk at work today. The LED blinks on or off per data cycle, so it is blinking at 10 Hz and the data is going out at 20 Hz:
Subscribe to:
Posts
(
Atom
)